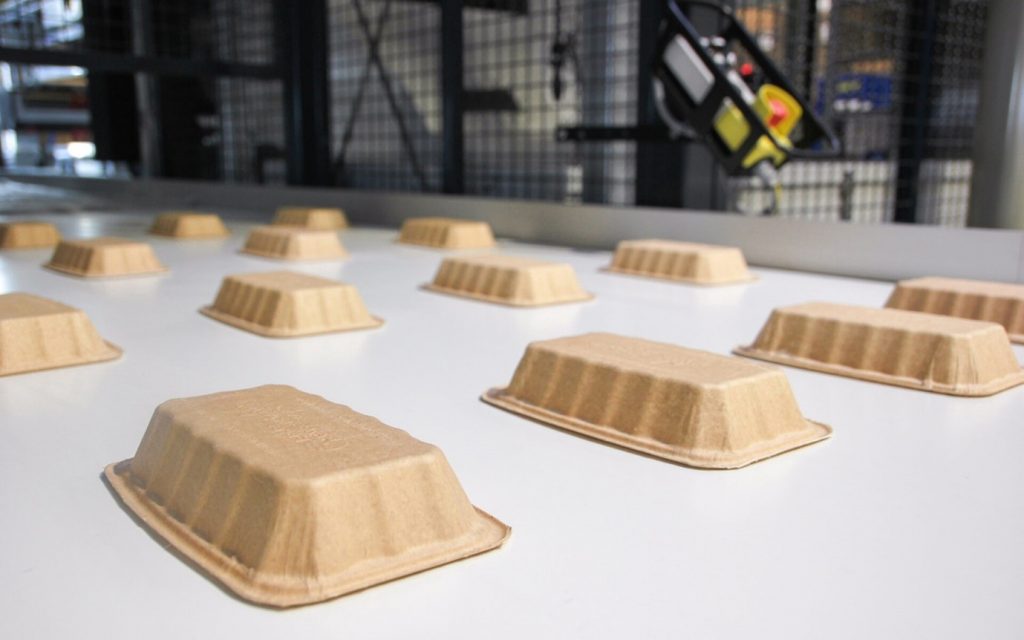
Dry Moulded Fibre production using PulPac’s technology. Photo from PulPac.
Plastic waste is a severe environmental issue, and the Western world is finally making some progress towards addressing it. This is likely due to countries like China and Malaysia curbing their acceptance of plastic waste from other countries, forcing many countries to reconsider their non-recyclable waste output. One possible solution for this waste problem are moulded fibres, and there likely is a moulded fibre package in your home right now in the form of an egg carton, which is generally formed via the wet moulding process. Innovation in the moulded fibre (also known as moulded pulp) industry has led to the design of the dry moulded fibre process (invented by PulPac), a new manufacturing method that produces a far superior, and more energy and water efficient, plastic alternative than its wet moulded relatives. It is achieved through taking renewable wood and plant pulp, milling it into fibres and then creating a mesh from them. Different chemical barriers can then be added to the mesh depending on the intended use of the item, this could be used to improve water and oil resistance, as well as strength. The products are then formed through the application of heat and pressure in a standard plate press. But is dry moulding the future of packaging?
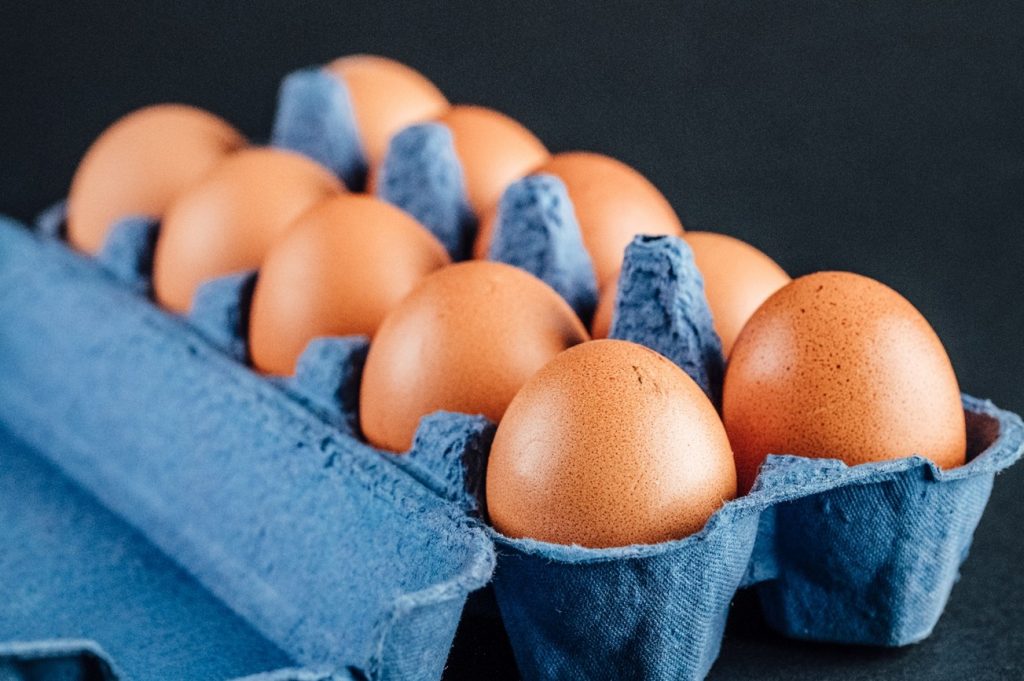
Wet Moulded Fibre egg carton. Image was obtained from Ivan Radic on Flickr.
To evaluate the dry moulded fibre (DMF) products, we need to compare them to plastic equivalents. Firstly, cycle times of DMF products (the amount of time to take a product from start to finish) now rivals plastics. PulPac’s method has a cycle time of just 3.5 seconds, which rivals even the quickest of injection moulded plastic methods, which can have cycle times between 2 seconds and 2 minutes. Dry moulded fibres also have 80-90% less carbon footprint compared to their plastic counterparts, and thanks to the innovations made by PulPac since its founding in 2015, the cost of production is now also competitive with plastic products. The downsides come in the form of strength, water resistance and many other properties that make plastic so effective, however the use of different chemical barriers in the DMF process is making these weaknesses dwindle fast. It should be noted that many of the barriers used at this point are not themselves renewable or biodegradable and hence appear to remove the main advantage of dry moulded fibres. Toxic per-and poly-fluoroalkyl substances (PFAS) are a commonly used, cost-effective chemical barrier that provides oil and grease resistance, high levels of PFAS in packaging poses a significant environmental and public health risk, especially as many are difficult to identify. Studies in Denmark on pulp-based take-out food packaging from other manufacturers found that some products contained over 60 times the levels stipulated by the Danish Veterinary and Food Regulatory Authority. Thankfully, progress is being made towards renewable, non-toxic chemical barriers and hence the use of PFAS and other similarly damaging chemical barriers will be phased out with time. Finally, flexibility in form is not quite up to plastics level yet, with dry moulded fibres being best applied to shallow containers, despite this, the technology is now applicable in many complex designs.
Its wet moulded counterpart uses large amounts of water and energy and generally produces less refined products lacking the continuous smooth surfaces seen in dry moulding, but currently is more appropriate in deeper more intricate products.
Another major competitor to dry moulded fibre comes from bioplastics, made from renewable biomass. Only around half of all bioplastics produced are biodegradable, and many of these require tightly controlled conditions in order to do so. Some will even release toxins and greenhouse gases during the decomposition process. Hence, it appears that the bioplastic industry has far more hurdles to clear than DMF.
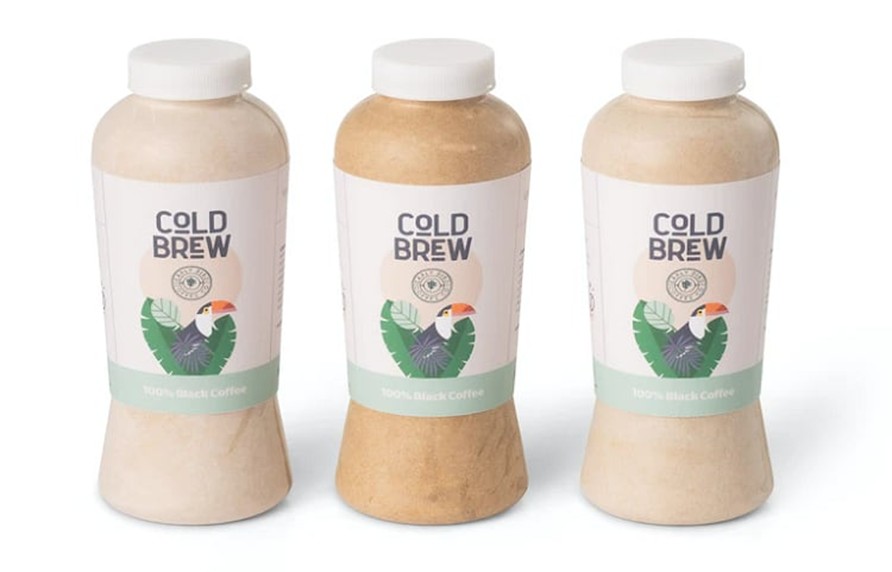
PA Consulting and PulPac’s prototype for the dry moulded fibre bottle. Photo from the Bottle Collective.
The advances in Dry Moulded Fibres made by PulPac implies that it is one of the better plastic alternatives today, and as they are a research-focussed company, not producing any end-user products themselves, the further development and improvement of this renewable packing material will likely be rapid. This is evidenced by their plan to release DMF bottles for liquids in 2025, which would be a world first. So, keep an eye out for this new emerging technology because its uptake will only increase with sustainability demands.